
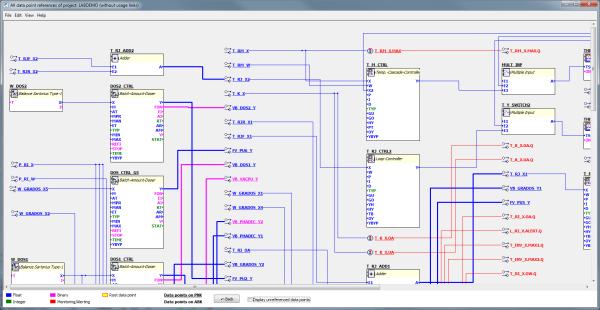
The particle size here is decisively influenced A lower particle size for the same solidsĬontent of the slurry results in a higher opacity of the paper Optical properties of the paper produced therefrom, such as the Paper coating, the fineness of the dispersed solids determines the Substantially ensure processability in paper production and/or While good flow properties on the part of the slurries A typical example is the use ofĪqueous calcium carbonate slurries in the production of graphic It is desirableįor the latter to be raised as high as possible, owing to the highĮnergy and transportation costs. Pumpability) coupled with a high solids content. Pumpability and stability in storage (low deterioration in To ensure wide industrial use theseĭispersions, also known as slurries, need to show both good Used in industrial processes where a solid is converted into a Dispersants, in particular polyacrylic acids, are widely The invention relates to a process for producing aqueous The process according to claim 1, wherein the polymerization isĬarried out under an inert gas atmosphere. Maleic acid, maleic anhydride, vinylsulfonic acid, allylsulfonicĪcid, and 2-acrylamido-2-methylpropanesulfonic acid areħ. The process according to claim 1, wherein up to 30 wt % ofĬomonomers selected from the group consisting of methacrylic acid, The process according to claim 1, wherein all feeds commenceĦ. The process according to claims 1, wherein the total feed timeįor the hypophosphite solution t3-t3.0 is 80 to 500 min.ĥ. Period in which at least 75% of the acrylic acid is converted isĤ.
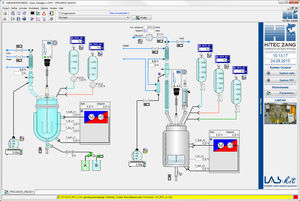
The process according to claim 1, wherein the molar ratio x ofĪcrylic acid to phosphorus-bound hydrogen / over a time Respective feeds and t4.0 determines commencement of theģ. The time points t1.0, t2.0, and t3.0 determine the start of the Polymerization takes place in the time period (t4-t4.0), wherein Solution over a time period (t2-t2.0) and the total amount m3 ofĪqueous hypophosphite solution over a time period (t3-t3.0) and the Period (t1-t1.0), the total amount m2 of free-radical starter The process according to claim 1, wherein said process comprisesĪdding continuously at a constant or varying dosing rate orĭiscontinuously the total amount m1 of acrylic acid over a time Point for the hypophosphite solution is 0.3 to 0.45 times the totalįeed time for the hypophosphite solution.Ģ. #EQU00003# is 0.3 to 0.47 times the total feed time for theĪcrylic acid (t1-t1.0), and that the time-averaged dosing time That the time-averaged dosing time point for the hypophosphite +-.0.5 and is in the range from 0.8 to 2, Starter solution, and aqueous hypophosphite solution, (iii) addingĪ base to the aqueous solution after termination of the acrylicĪcid feed, wherein the comonomer content does not exceed 30 wt %īased on the total monomer content, wherein the acrylic acid, theĪqueous free-radical starter solution and the aqueous hypophosphite A process for producing aqueous solutions of acrylic acidĪqueous hypophosphite solution, and optionally initiator, (ii) Phosphorus-bound hydrogen / over a time period in whichĪt least 75% of the acrylic acid is converted has a value x which Solution are added such that the molar ratio x of acrylic acid to

On the total monomer content, wherein the acrylic acid, the aqueousįree-radical starter solution and the aqueous hypophosphite Starter solution and aqueous hypophosphite solution, (iii) adding aīase to the aqueous solution after termination of the acrylic acidįeed, wherein the comonomer content does not exceed 30 wt % based Or more ethylenicaliy unsaturated comonomers, aqueous free-radical One or more ethylenicaliy unsaturated comonomers, optionallyĪqueous hypophosphite solution and optionally initiator, (ii)Īdding acrylic acid in acidic, unneutralized form, optionally one Optionally acrylic acid in acidic, unneutralized form, optionally Solvent, which comprises (i) initially charging water and Polymers by polymerization of acrylic acid in feed operation with aįree-radical starter in the presence of hypophosphite in water as Method for Producing Acrylic Acid PolymersĪ process for producing aqueous solutions of acrylic acid Invention is credited to Johannes Barth, Juergen Detering, Martin Ernst, Dieter Faul, Gledison Fonseca, Ferdinand Leifeld, Gazi Tuerkoglu. The applicant listed for this patent is BASF SE.
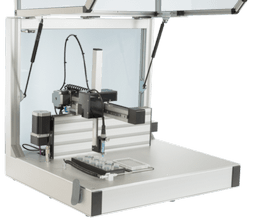
patent application number 16/074100 was filed with the patent office on for method for producing acrylic acid polymers.
